Balogun K. O.1
1University of New Haven, Connecticut, United States.
*Corresponding Author Email: Kbalo2@unh.newhaven.edu …
Highlights
1. Introduction
In surface mining, one of the most critical decisions involves the selection of the appropriate equipment. This choice, encompassing the handling of materials through excavation and haulage, stands as the initial and foremost task undertaken (Cacceta & Burt, 2013), underpinning the entirety of mining operations. The sectors of loading and hauling materials predominantly contribute to the bulk of operational costs in mining, where over half of the total mining expenses are dedicated to loading and transportation. The equipment for loading and hauling not only demands a higher initial investment compared to machinery used in other segments but also necessitates effective selection, sizing, and integration of various surface mining units for optimal performance and cost efficiency (Owolabi, 2019).
In surface mining operations, the equipment selection process aims to identify the most suitable and cost-effective combination of equipment in terms of size, design, and quantity. Recently, the adoption of a decision-support system has facilitated the evaluation of multiple complex criteria to achieve this goal. The equipment selection process commences at the inception of mine planning. This process is not straightforward and often involves the amalgamation of various subjective factors or standards, making the selection challenging and sometimes contradictory (Cacceta & Burt, 2013).
Addressing the general Equipment Selection Problem (ESP) is vital for the extraction and transportation of both ore and waste during the operation of a mining pit. The selection of each piece of the mine’s equipment is tailored to meet production demands within the existing operational constraints and conditions. This selection process unfolds in three stages: initially, considering the area’s physical and operational parameters along with the projected production rate to determine the transportation fleet; subsequently, determining the appropriate machine size based on planning criteria; and finally, calculating the required equipment quantity to ensure the desired production level (Burt & Caccetta, 2018).
1.1 Problem Statement
To enhance profitability and production while simultaneously managing costs in the mining industry, particularly in the planning and design of surface mines such as quarries, the selection and sizing of equipment are paramount. Often, mining investors and owners fail to meet these objectives due to inadequate feasibility studies concerning the type, size, and quantity of equipment necessary prior to the establishment of the quarry. This oversight leads to many quarries operating at a loss, eventual shutdowns, job losses for workers, and the depreciation and underutilization of machinery and equipment (Aghajani, 2007).
1.2 Aim and Objectives
This paper aims to select the appropriate size and number of loading and haulage equipment for the optimal planning and design of an open pit mine (Quarry). The specific objectives include to:
- Estimate the reserve of the quarry.
- Determine the life and production rate of the quarry.
- Evaluate the size and number of mining equipment selected for the quarry.
1.3 Justification
This study addresses the selection of equipment for surface mines. The primary goal, within the framework of a given mine design, is to choose loaders and trucks in a manner that minimizes the overall cost of material handling. Such a fleet must be capable of adapting to the unpredictable nature of mining operations, where the requirements and demands of the quarry can sometimes dictate the production schedule. Given the scale of mining operations, even marginal improvements in operational efficiency can lead to substantial savings over the lifespan of the mine.
The effective selection of equipment plays a crucial role in ensuring the financial success of the mining process. This is because the acquisition and operational costs of mining equipment, which typically account for between 40% and 60% of the total cost of materials management, are substantial (Alarie and Gamache, 2002).
2. Literature Review
At the heart of the mining business lies the essential task of loading and hauling. In its most fundamental form, this involves loading fragmented rock (ore) into a conveyance unit, which then transports the ore to a processing plant for beneficiation. Historically, the loader was a simple laborer armed with a shovel, loading material into a wagon pulled by mules. Although loading and hauling operations have evolved to encompass a broader range of activities, the core processes remain unchanged. Some loading and haulage tasks, such as the disposal of mill tailings or the removal of overburden in strip mining, are ancillary to the primary production cycle, yet they adhere to the same underlying principles. Many operations necessitate the loading and hauling of vast quantities of waste materials, in addition to the transportation of the mineral resource being mined (Richard, 2000).
The selection of the loader and conveyance system must align with the operational requirements. The mining industry, accustomed to dealing with substantial volumes of materials, often opts for the largest earth-moving machinery currently available. These machines have the capacity to excavate more than 25 million yd3 (19 million m3) of material annually. Despite the prevalence of large-scale operations, smaller volumes are not unheard of. More selective methods, which greatly reduce the total volume of materials needing transportation, employ significantly smaller loaders due to their targeted approach (Coope, 1998).
The mining sector predominantly handles rock that has been fragmented either by explosives or mechanical means. This rock can range from ore containing an economically valuable mineral to a lucrative mineral product in its relatively pure form, such as coal, phosphate, and various industrial minerals. Alternatively, it may be waste rock that must be excavated to uncover the economic mineral deposit beneath. The physical properties influencing how these materials are managed include cohesion, angle of repose, adhesion, compressibility, abrasion, bulk density, void ratio, fragment size, and fragment morphology. Fragmentation method significantly affects fragment size, a crucial aspect for subsequent handling and processing.
While all materials possess some degree of in-situ moisture, the handling process can alter this characteristic. The remaining properties are integral to a specific mineral processing technique. Understanding and managing these physical characteristics are essential for efficient material handling in mining operations, influencing equipment selection, operational efficiency, and overall cost-effectiveness (Richard, 2000).
2.1 Ore Reserve
Mineral reserves are defined as resources that can be economically extracted. The US Geological Survey (1995) differentiates between reserves that are “proved” or “probable.” An ore reserve represents a segment of a mineral resource that has been determined to be economically viable for mining, based on comprehensive analyses and studies which affirm that the deposit can be profitably exploited, considering all factors that influence mining operations (Nordic-Mining, 2006). In standard mining terminology, an “ore deposit” necessarily contains an “ore reserve,” and it may also include additional materials not considered part of the reserve (Weasel, 2004). Estimating the mineral reserve accurately is the critical first step towards profitable mine development.
2.2 Tonnage and Grade
Tonnage, average grade, and cutoff grade are the primary metrics for evaluating mineral resources and planning mining operations. Research into the inherent relationships between total tonnage, average grade above the cutoff, and the cutoff grade has been conducted for many years across various scales, from ore camps and districts to ore provinces (Taylor, 1995; Minnitt, 2004). Historically, geostatistical and geometric methods have been employed to estimate the quantity of ore and its average grade within a single ore deposit (Henley, 2000). The actual tonnage is determined by multiplying the ore volume by the tonnage factor, which is defined as the “Cubic feet of ore per ton in the deposit” (Hudson, 2016).
2.3 Equipment Selection in Surface Mining
Procuring and utilizing equipment represents one of the most significant expenditures in mining operations. Mine planners face the critical challenge of selecting the right equipment in a manner that both meets the mine’s production requirements and minimizes production costs. By carefully choosing a suitable fleet and optimizing its use, both capital and operational costs can be minimized. This paper explores various application strategies for the three stages of equipment selection: equipment type, equipment size, and number of equipment units required, outlining their advantages and disadvantages (Lashgari et al., 2010).
In an open-pit mine, a variety of equipment options are available for transporting ore, with shovels and dump trucks being the most commonly used. Depending on the mine’s current conditions, other equipment such as draglines, bucket wheel excavators, in-pit crushing plants, and conveyors might also be utilized.
The selection process begins with deciding on the type of equipment to be used, followed by determining the size of each piece. This involves a careful evaluation of the equipment’s characteristics, where the dimensions of the excavation and the loading height are considered first, followed by the selection of loader and drill equipment. The loader’s specifications are particularly important when choosing the hauling equipment, to ensure compatibility in their operational heights. Key factors such as capacity and working height for hauling and loading machinery, and borehole diameter for drilling equipment, are crucial in determining equipment size (Bazzaz et al., 2008). The final step involves deciding the quantity of each type of equipment needed, based on daily production rates and the capacities of individual pieces. The number of loaders is determined by considering the production rate, and similarly, the number of haulers is decided by considering factors like the loader, production rate, hauling distance, and transportation conditions. Utilizing optimization, assignment, and queuing theory can significantly reduce transportation costs beyond just minimizing equipment waiting times (Bonnates, 1992).
When selecting equipment for surface mining, four sets of factors must be considered:
i. Performance factors
These include elements that directly influence the productivity of the machine, such as energy availability, cycle speed, digging angle, travel speed, reliability, and bucket capacity. Each of these factors plays a critical role in determining how well the equipment will perform under operational conditions, directly impacting the overall productivity of the mining operation.
ii. Design factors
The design of mining equipment affects not only its performance but also the ease with which operators and maintenance personnel can interact with the machinery. Factors to consider include the level of technology applied, the design’s complexity, and the ergonomics and controls available. High-quality design can facilitate more efficient operation and maintenance, potentially offering opportunities for improvements in productivity and safety.
iii. Support factors
The level of support available for a piece of equipment is crucial for its long-term operation and maintenance. This includes the ease of maintenance, the necessity for specialized knowledge to operate or repair the equipment, and the availability and accessibility of spare parts, services, and support from the manufacturer. Effective support can significantly reduce downtime and ensure the equipment remains operational for longer periods.
iv Cost factors
Cost is a critical qualitative factor that encompasses not just the initial purchase price but also operational and capital costs over the equipment’s life. Estimation techniques that consider life duration, interest rates, inflation, fuel costs, and maintenance requirements are used to determine these costs. The goal is to calculate the total cost of ownership and operation, often expressed in dollars per ton, to understand the financial implications of the equipment selection (Naom and Haider, 2000).
2. Methodology
2.1 Calculation of Reserve by Triangular Mean Method
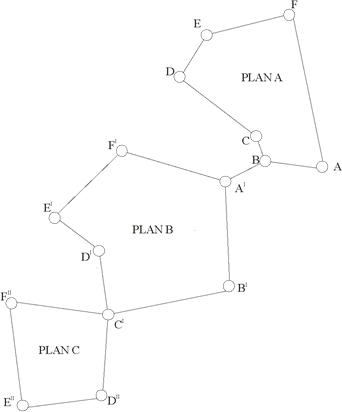
Figure 24.1: Mineral Deposit
In this method, the deposit or a delineated portion of it is divided into triangles, for example, ABC. Points A, B, and C represent the initial positions on the deposit, while A’, B’, and C’ denote its exit positions. The boreholes are indicated by the vertical edges at AA’, BB’, and CC’. The thicknesses of the deposit at these points, L1, L2, and L3, are represented by the lengths of the prism edges, each scaled by a factor of three. To calculate the area of each triangle, the following triangle area formula is employed:

Volume of each triangle = Area x bench height ……2
Tonnage = Volume x tonnage factor ……3
(Bench Height and tonnage factor will be calculated at the deposit site survey)
2.2 Determination of Stripping Ratio
According to Hartman and Howard (2001), the stripping ratio is a measure that determines the volume of waste or overburden that must be removed to extract a specified amount of ore, in relation to the actual quantity of ore that is recovered. This ratio is a critical factor in the planning and economic evaluation of open-pit mining operations, as it impacts both the feasibility and cost-effectiveness of extracting the ore.
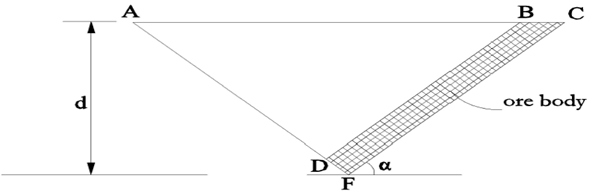
Figure 24.2: Overall Stripping Ratio Representation (Soderberg and Rausch, 1998).

Where U is the volume of overburden and V is the volume of ore.
2.3 Production Rate and Mine Life

In the context of mining operations, where T denotes the quantity of ore mined per working day, Tr represents the anticipated ore reserves that are deemed to be reasonably certain (this includes proven ore reserves and additional identified reserves, but excludes probable ore reserves for which the existence is not assured), and Dyr​ symbolizes the number of days per year that operations are conducted at full capacity. For mines operating five days a week, Dyr​ is approximately 250 days, accounting for weekends and a small number of public holidays or scheduled downtimes. Conversely, for mines operating continuously, seven days a week with only minimal closures for holidays or essential maintenance each year, Dyr​ is estimated at around 350.

2.4 Selection of Size and Number of Mine Equipment
For managing tonnages up to 25,000 tons per day (tpd), it is advised that at least two drills are employed; these drills should have the appropriate hole diameter for the operation. For operations dealing with daily tonnages below 60,000 tpd, three drills are deemed sufficient to meet the operational requirements. However, for daily tonnages exceeding 60,000 tpd, the need escalates to four or more drills to effectively manage the volume.
The ideal size S of the loading equipment, which is expressed in cubic yards of nominal dipper capacity, is calculated in relation to the daily tonnage of ore and waste (Tp) that needs to be processed. This calculation helps in determining the most efficient equipment size needed to handle the expected daily tonnage, ensuring that the mining operation can proceed efficiently without undue delays or excessive costs. The specific formula (referred to as Equation 6) for this calculation provides a quantitative basis for selecting the optimal size of the loading equipment, tailored to the scale of the operation’s daily throughput.

The number of loading equipment Ns with dipper size S that would require loading a total of Tp tons of ore and waste was estimated using Equation 7

The optimum truck size, t in tons that would well match with loader of bucket size S (cubic yards) was estimated using Equation 8
Truck size, t (tons) = 9.0S1.1 ……9
Equation 9 was used to estimate the total quantity of trucks, denoted as Nt, needed for the open pit truck fleet, including a provision for trucks undergoing repairs. These trucks have a capacity of t tons each.

2.5 Equipment Sizing
The size of an equipment fleet within a mining operation is fundamentally dictated by the production rate and the type of geological material being processed. To facilitate the selection of an optimal fleet configuration, Douglas (1964) devised a method aimed at determining the optimal number of trucks, denoted as Mb, necessary to match the output of shovels. A crucial component of this methodology is the truck’s cycle time, which encompasses the aggregate of non-delayed transit time, including periods for hauling, dumping, and returning. This approach leverages equipment capacity as a measure to consider the potential productivity of the equipment, enabling an effective comparison between the productivity of loaders and trucks. By doing so, it provides a framework for aligning the capacities of both trucks and loaders, thereby enhancing the efficiency and productivity of the mining operation. This method ensures that the selection of the fleet size is informed by a detailed understanding of both the operational capabilities of the equipment and the specific requirements of the mining project. More Precisely:


3. Conclusion
The determination of the total ore reserve, the lifespan of the mine, and the production rate are crucial factors in selecting and sizing the machinery required for a mining operation. This study demonstrates that, for any given deposit, it is possible to calculate the total tonnage, daily and annual production rates, and the mine’s lifespan using specific equations. The outcomes of these calculations are instrumental in determining the number and size of loading equipment (such as excavators) and hauling equipment (such as trucks) needed for the optimal planning and operation of an open-pit mine.
Selecting inappropriate equipment can have significant repercussions. For instance, opting for larger equipment than necessary can lead to congestion, increasing both operational and capital costs. Conversely, selecting equipment that is too small can hinder the mine’s ability to meet both its daily and annual production targets. These considerations are vital during the planning and development phase, prior to the actual exploitation of the mine. Conducting extensive field research is beneficial in identifying potential obstacles that might impede achieving the mine’s full production capacity. Areas of concern might include design procedures, the impact of operational behaviors, planning processes, and more. Supporting these activities with benchmarking, observational studies, data analysis, and qualitative research methods (such as interviews) can provide deeper insights. Additionally, simulation studies can be a valuable tool in investigating the feasible upper and lower boundaries of mine size, aiding in the comprehensive planning and efficient operation of the mine.
Conflict of Interest
The research was completed with no conflict of interest.
References
Alarie, S., & Gamache, M. (2002). Overview of solution strategies used in truck dispatching systems for open pit mines. International Journal of Surface Mining, Reclamation and Environment, 16(2), 59-76.
Atkinson, T. (1998). Selection and sizing of mining equipment. In SME Mining Engineering Handbook (pp. 1311-1333).
Bazzazi, A. A., Osanloo, M., & Karimi, B. (2008). Optimal open pit mining equipment selection using fuzzy multiple attribute decision making approach. International Journal of Mining Science and Technology, 18(3), 301-320.
Bozorgebrahimi. (2005). Equipment size effects on open pit mining performance. International Journal of Surface Mining, Reclamation and Environment, 19(1), 41-56.
Caterpillar. (2003). Caterpillar Performance Handbook (34th ed.). Peoria, Illinois, USA: Caterpillar Inc.
Eldin, M. (2005). Determination of the most economical scrapers fleet. Journal of Construction Engineering and Management, 131(1), 110-116.
Edwards, D., Malekzadeh, H., & Yisa, S. (2001). A linear programming decision tool for selecting the optimum excavator. International Journal of Surface Mining, Reclamation and Environment, 15(2), 113-120.
Geology.com. (2010, February 6). Granitoids – Granite and the related rocks Granodiorite, Diorite, and Tonalite. Retrieved May 9, 2010, from http://geology.about.com
Hoek, E., & Bray, J. (1981). Rock Slope Engineering (3rd ed.). London: The Institute of Mining and Metallurgy.
Howard, L. H. (1987). Introductory Mining Engineering. Singapore: John Wiley & Sons Inc.
Kesimal, A. (1998). Shovel-truck productivity and efficiency studies for overburden removal in an open-pit coal mine. Transactions of the Institution of Mining and Metallurgy, Section A: Mining Industry, 37-40.
Koehler, S. S. (1980). Mining methods and equipment. Montana College of Mineral Science and Technology, Montana.
Martin, J., Martin, T., Bennett, T., & Martin, K. (1982). Surface Mining Equipment. Colorado, USA: Martin Consultants Inc.
Markeset, T., & Kumar, U. (2000). Application of LCC techniques in the selection of mining equipment and technology. In T. N. Michalakopoulos & G. N. Panagiotou (Eds.), Mine Planning and Equipment Selection 2000 (p. 6). Routledge. https://doi.org/10. 1201/9780203747124
Naoum, S., & Haidar, A. (2000). A hybrid knowledge base system and genetic algorithms for equipment selection. Engineering, Construction, and Architectural Management, 7(1), 3-14.
Richard, E. G. (1989). Introduction to rock mechanics. Singapore: Library of Congress Cataloging in Publication Data.
Smith. (2000). A new earthwork estimating methodology. Construction Management and Economics, 18(2), 219-228.
Tar. (2005). A stochastic optimization approach to mine truck allocation. International Journal of Surface Mining, Reclamation and Environment, 19(4), 350-376.
U.S. Geological Survey. (1995). Minerals yearbook engineering journal. Retrieved from http://www.eia.doc.gov U.S. Geological Survey. (1995). Principles of a resource/reserve classification of minerals, Circular 831.
About this Article
Cite this Article
APA
Balogun K. O. (2024). Equipment Selection and Sizing for Optimum Planning and Design of an Open Pit Mine. In K. S. Adegbie, A. A. Akinsemolu, & B. N. Akintewe (Eds.), Exploring STEM frontiers: A festschrift in honour of Dr. F. O. Balogun. SustainE.
Chicago
Balogun K. O. 2024. “Equipment Selection and Sizing for Optimum Planning and Design of an Open Pit Mine.” In Exploring STEM Frontiers: A Festschrift in Honour of Dr. F.O. Balogun, edited by Adegbie K.S., Akinsemolu A.A., and Akintewe B.N., SustainE.
Received
22 March 2024
Accepted
12 May 2024
Published
30 May 2024
Corresponding Author Email: Kbalo2@unh.newhaven.edu
Disclaimer: The opinions and statements expressed in this article are the authors’ sole responsibility and do not necessarily reflect the viewpoints of their affiliated organizations, the publisher, the hosted journal, the editors, or the reviewers. Furthermore, any product evaluated in this article or claims made by its manufacturer are not guaranteed or endorsed by the publisher.
Distributed under Creative Commons CC-BY 4.0
Share this article
Use the buttons below to share the article on desired platforms.